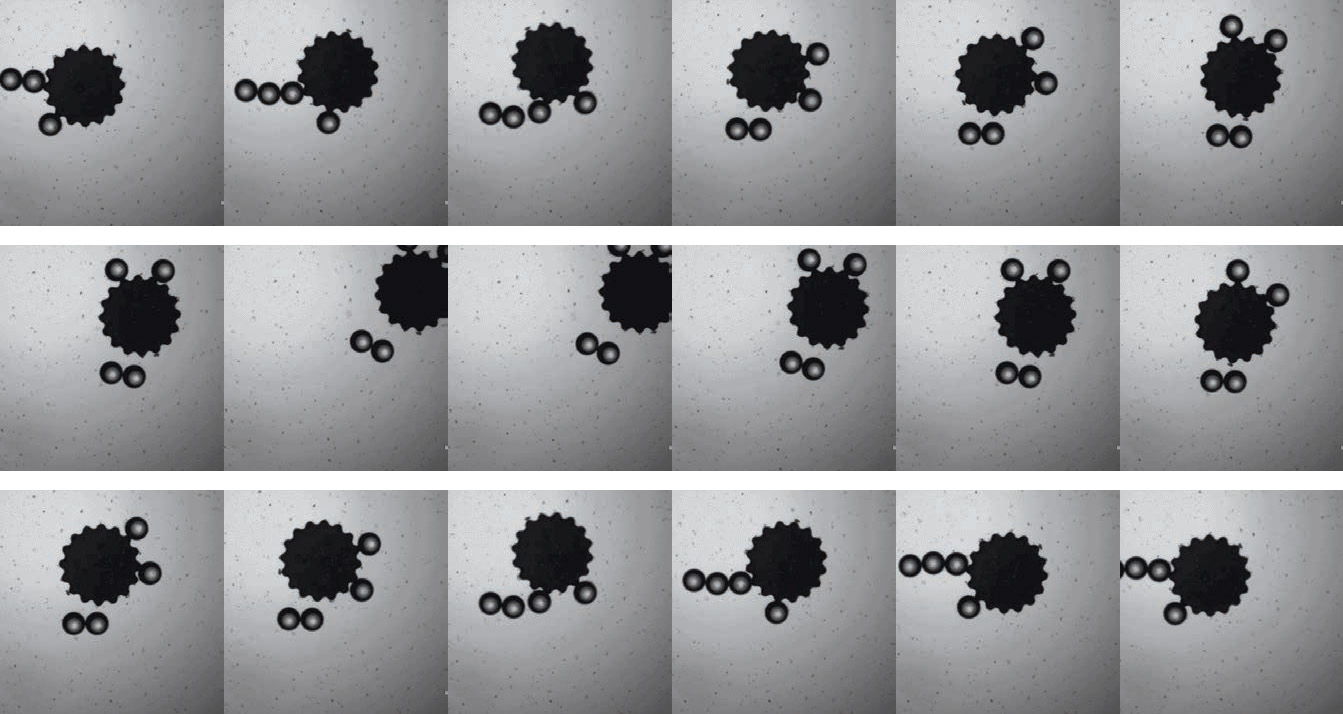
Breakthroughs
Micro Manipulators
Controlling microscopic processes is inherently challenging. The everyday tools we use to manipulate matter on the macroscale can’t simply be shrunk down to the size of a cell, and even if they could, the physical forces they rely on work differently when their targets are measured in nanometers. But while it’s no easy feat, attaining this type of control would pay enormous dividends: from transporting drugs to tumors for precise therapies, to making functional materials out of microscopic building blocks, to enabling new kinds of displays and sensors.
One approach for controlling these types of processes is via microrobots.
We typically think of robots as computerized machines like those on assembly lines or in warehouses, programmed to move cargo and to build complex structures like automobiles and cellphones. However, programming a device smaller than a microchip presents another kind of challenge. Robots on this scale need to be designed in a completely different way than their bigger counterparts.
Since they’re too small for their own onboard computers, microrobots’ movements are controlled by an external magnetic force. And to manipulate equally small cargo, they need to take advantage of the different physical and chemical laws that rule the microscale.
At those sizes, every object is greatly influenced by the molecules surrounding it. Whether they are surrounded by gas, like the ambient atmosphere, or dispersed in a liquid, micro robots must be designed to exploit this influence, a concept known as “physical intelligence.”
Kathleen Stebe, Richer & Elizabeth Goodwin Professor in Chemical and Biomolecular Engineering and Mechanical Engineering and Applied Mechanics, Tianyi Yao and Qi Xing Zhang, graduate students in her lab, and collaborators at the University of Ljubljana, Slovenia, are establishing some of the fundamentals of physically intelligent microrobots, publishing a pair of groundbreaking papers earlier this year.
Their studies investigated magnetic micro robots swimming through nematic liquid crystals ( NLC s), the fluid that makes up each pixel in a liquid crystal display. Colloidal systems like these, where one material is dispersed through another, can give even the simplest microrobots a way of doing work; rather than arm-like mechanical grippers you would find on an assembly line, they can extend “force fields” of elastic energy by altering the arrangement of molecules around them. “Nematic liquid crystals exist as a special phase, a structured fluid that is neither liquid nor solid,” says Stebe. “NLCs consist of elongated molecules that self-align in a configuration that requires the least amount of energy. Think of shaking a pan of rice; the grains all align. When you disturb the nematic alignment by introducing microrobots or colloidal cargo, you get really interesting dynamics that you don’t see in water, for example.”
In one study, Stebe and her colleagues deployed X-shaped microrobots, each roughly a twentieth of a millimeter across, and showed how they could pick up and move spherical particles in complicated ways. Though their four stumpy arms can’t grab this cargo on their own, their specially designed shape disrupts the surrounding NLCs in such a way that the particles are attracted to the microrobot’s edges.
The team also demonstrated more advanced maneuvers, flicking particles away with a twist, or using the geometry of stationary structures in the environment to deposit them in specific locations.
The team’s other study answered even more fundamental questions about the microrobots’ swimming and gripping abilities. There, they used a robot with an even simpler shape — a flat disk — and a simpler form of magnetic control. By rotating the magnetic field back and forth, they saw that one side of the disk would lift, creating a disruption in the liquid crystal pattern under- neath it. This created an energy gradient that the microrobot could follow, propelling itself forward without needing to be dragged along by the external magnetic field.
Stebe and her team are now able to imagine real-world applications for this technology in the optical device industry as well as in many other fields.
“Together with dedicated colleagues and graduate students, we have been working hard on this technology and are excited to see years of work come to fruition,” she says. “We are now standing on the edge of real applications and ready to explore.”
Microrobots in Your Mouth
Applications for tiny robots are diverse, requiring the design of each robotic system to be as unique as the problem it aims to solve. At the Center for Innovation and Precision Dentistry (CiPD), directors Stebe and Hyun (Michel) Koo, Professor in Penn Dental Medicine, look to microrobots to help clean, sample and diagnose plaque buildup and infections in the mouth. Together with Edward Steager, senior research investigator at Penn Engineering, they designed physically intelligent, magnetically controlled iron oxide nanoparticles that can move through the complex anatomy of the root canal or act as a swarm to brush and floss your teeth.
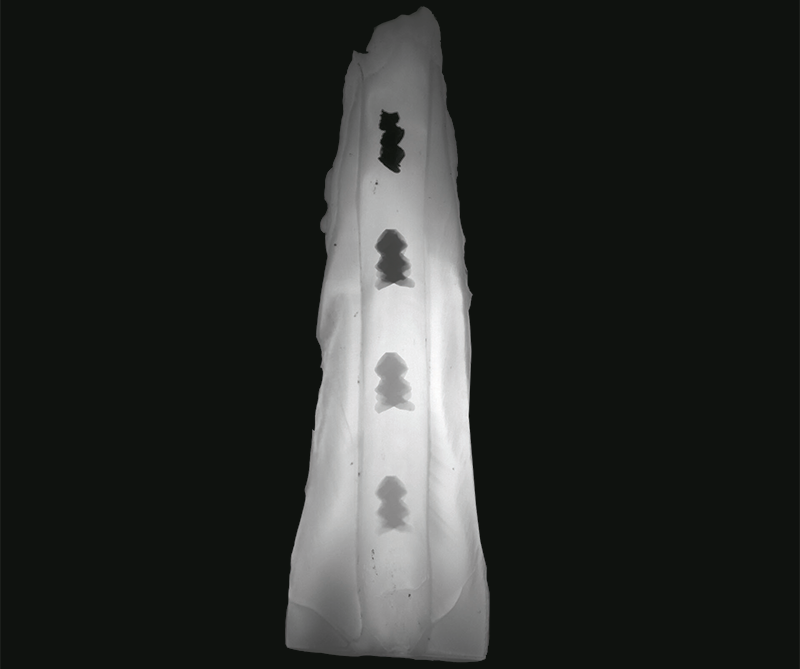
Root canal operations are common, but not highly efficient or very comfortable. Koo and Steager developed microrobots embedded with iron oxide nanoparticles con- trolled by an external magnet that can move through the root canal.
Along their journey, these microrobots remove plaque, take samples and deliver targeted therapies. This technology removes the need to drill through the tooth to reach the infected area as is done in traditional root canal procedures.

But before a patient needs a root canal procedure, microrobots can aid them in everyday dental hygiene.
The same nanoparticles can form a swarm in the shape of bristles, like a toothbrush, or elongated strings, like floss, to mechanically scrub and sweep plaque from teeth. The particles also chemically remove plaque through a catalytic reaction triggering a production of antimicrobials, providing multiple forms of attack on the biofilm in the patient’s mouth.
Text by Melissa Pappas.
Inside Engineering
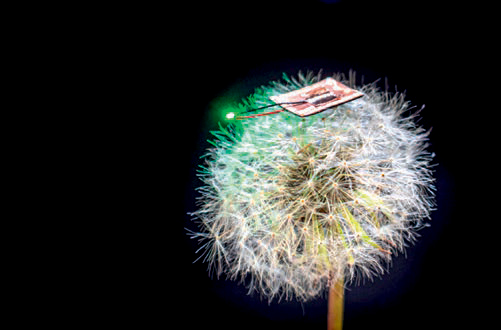
QUADRUPLING MICROBATTERY
ENERGY DENSITY
James Pikul, Assistant Professor in Mechanical Engineering and Applied Mechanics, and his team have found a new way to build and package microbatteries that maximizes energy density even at the smallest sizes.
Mobile electronics like robots and wearables are pushing batteries to be smaller and lighter, properties at odds with the need to make them last longer and be more durable. Working against this need is the fact that energy density gets substantially harder to improve upon as a battery gets smaller, partially because larger portions of a battery’s footprint must be devoted to protective packaging.
Confronted with this challenge, Pikul and his group developed a new kind of current collector and cathode that together act as both an electron conductor and the packaging that prevents water and oxygen from getting into the battery.
Weighing about as much as two grains of rice but with the energy density of a much larger, heavier battery, this packaging-free design could enable a host of otherwise impossible electronics.
This increases the fraction of materials that store energy and reduces the need for non-conductive packaging that normally protects a battery’s sensitive internal chemicals.
Full story on Penn Engineering Today.
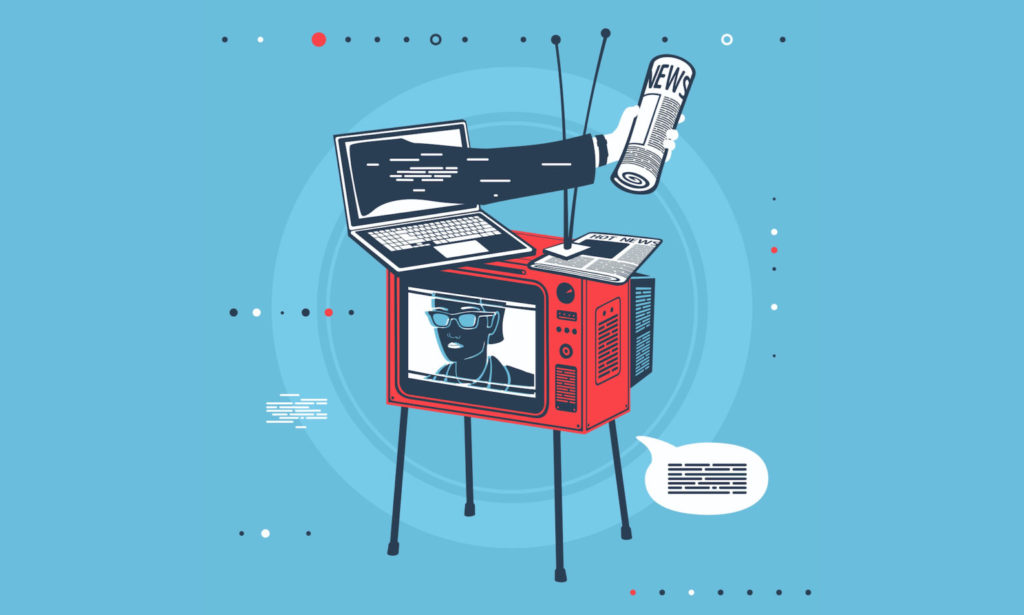
TV News Drives Division
Contrary to what many believe, social media and other online outlets are not the main source of news echo chambers and their resulting divisive- ness in the United States.
Research by Duncan Watts, Stevens University Professor in Computer and Information Science with appointments in Penn’s Annenberg School for Communication and in Wharton, and his collaborators has shown that just 4% of Americans are in what can be called echo chambers online, contrasted with 17% of Americans who are in such echo chambers with their TV news consumption.
The team also found that just 21% of Americans are responsible for 60% of news consumption, meaning that individuals in TV news echo chambers watch more news than those who are not, and that they are more likely to stick around as viewers: A partisan TV news diet has a 25% chance of lasting six months; online, it has only a 5% chance of lasting that amount of time.
Additionally, Watts and his group show that millions of TV viewers only watch content from a single source, such as CNN, MSNBC or FOX . This means that if information from one of those sources is misleading or problematic, the effects can be far worse among TV audiences than among people who consume that channel’s content via social media news algorithms, since online audiences tend to have more varied news diets to balance out their consumption.
Through their work, Watts and his collaborators hope to call more attention to the issue of TV news and partisanship. The findings also note that while 17% of the population represents millions of Americans, it is encouraging to learn that it isn’t a majority and that most people are still consuming multiple sources of TV news.
Full story on Penn Engineering Today.
Departmental Highlights
Bioengineering
Encrypted Peptides as Antibiotics
César de la Fuente, Presidential Assistant Professor, and his research group have used an algorithm to pinpoint specific sequences in our protein code that reveal encrypted peptides with antimicrobial properties that could act as naturally occurring antibiotics within our own bodies.
Chemical and Biomolecular Engineering
Shrinking Separation’s Carbon Footprint
In the lab of Chinedum Osuji, Eduardo D. Glandt Presidential Professor and Chair, researchers are decreasing the energy needed for chemical separation by leveraging energy-efficient organic separations that use nanofiltration and self-assembling membranes.
Computer and Information Science
Unmasking Social Bots
Using state-of-the-art machine learning and natural language processing techniques, Lyle Ungar, Professor, has collaborated to show that social media bots’ similarity to one another reveals their artificial nature, suggesting a new detection strategy.
Electrical and Systems Engineering
2 Billion Images Per Second
Firooz Aflatouni, Associate Professor, and his lab have created the first scalable chip that classifies and recognizes images almost instantaneously, enabling more sophisticated image classification, such as identifying moving objects, 3D object identification, or classification of microscopic cells in the body.
Materials Science and Engineering
A New Class of Polymers
A team led by Karen Winey, Harold Pender Professor, demonstrated that “multiblock” copolymers can produce exceptionally ordered patterns in thin films — achieving spacings smaller than three nanometers — which could be used for nanopatterning, a way of manufacturing microscopic components for computer chips.
Mechanical Engineering and Applied Mechanics
Starshot Lightsail
Rather than using solar energy, the lab of Igor Bargatin, Associate Professor, has reimagined the lightsail concept into a sail that would be constructed of nanoscopically thin materials and powered by light from a laser on Earth, designing the sail’s shape and composition so it would not melt or tear during acceleration